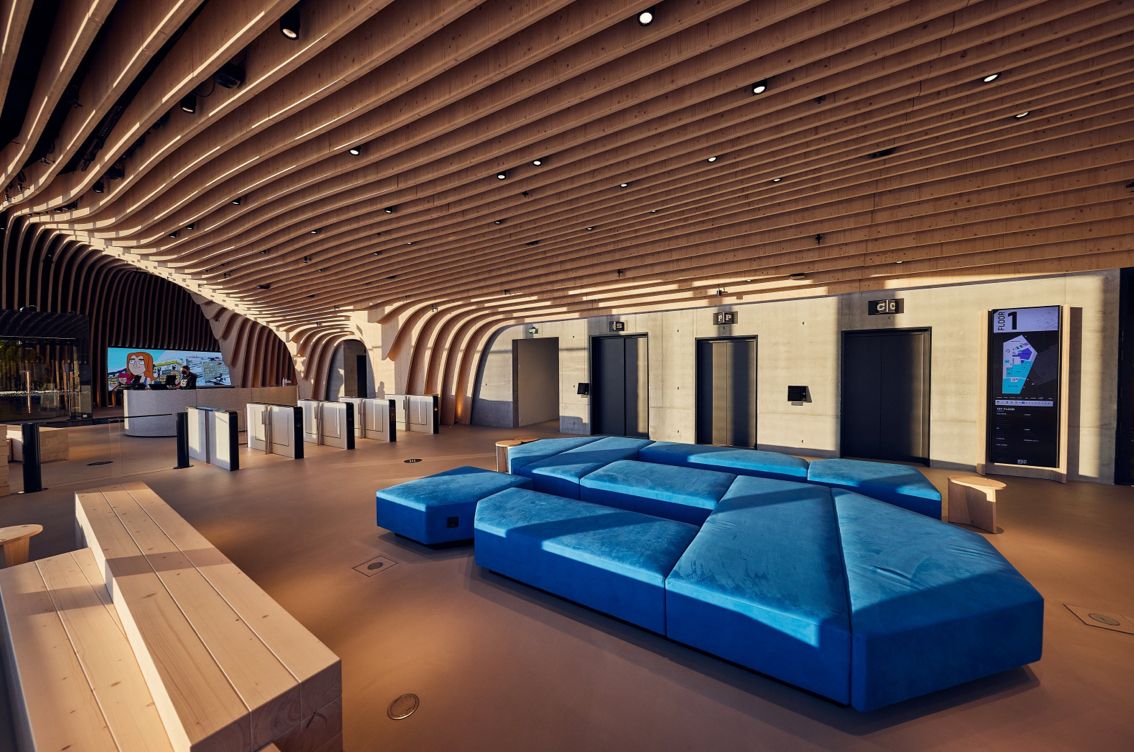
Why woodn't you?
A material we have used for thousands of years could become more important.
Summary: Developers in Finland are increasingly swapping concrete and steel for wood. With 75 percent of Finland covered by forests, wood is a readily available material for construction. We also look at things to consider, such as regulation, and other alternative materials.
Why this is important: Timber use in low rise residential buildings is already increasing. As it starts to be used in higher constructions, can buildings standards and the number of appropriately qualified people keep up?
The big theme: The built environment is an important sustainability theme, both as an integral part of societal existence but also a major decarbonisation (40% of energy-related GHG emissions) and resource consumption problem (40% of global raw materials) that needs investor attention. Including residential and commercial buildings, communal areas such as parks and supporting infrastructure such as energy networks and water supply, it can have significant impacts on our health, well-being and equity & inclusion.
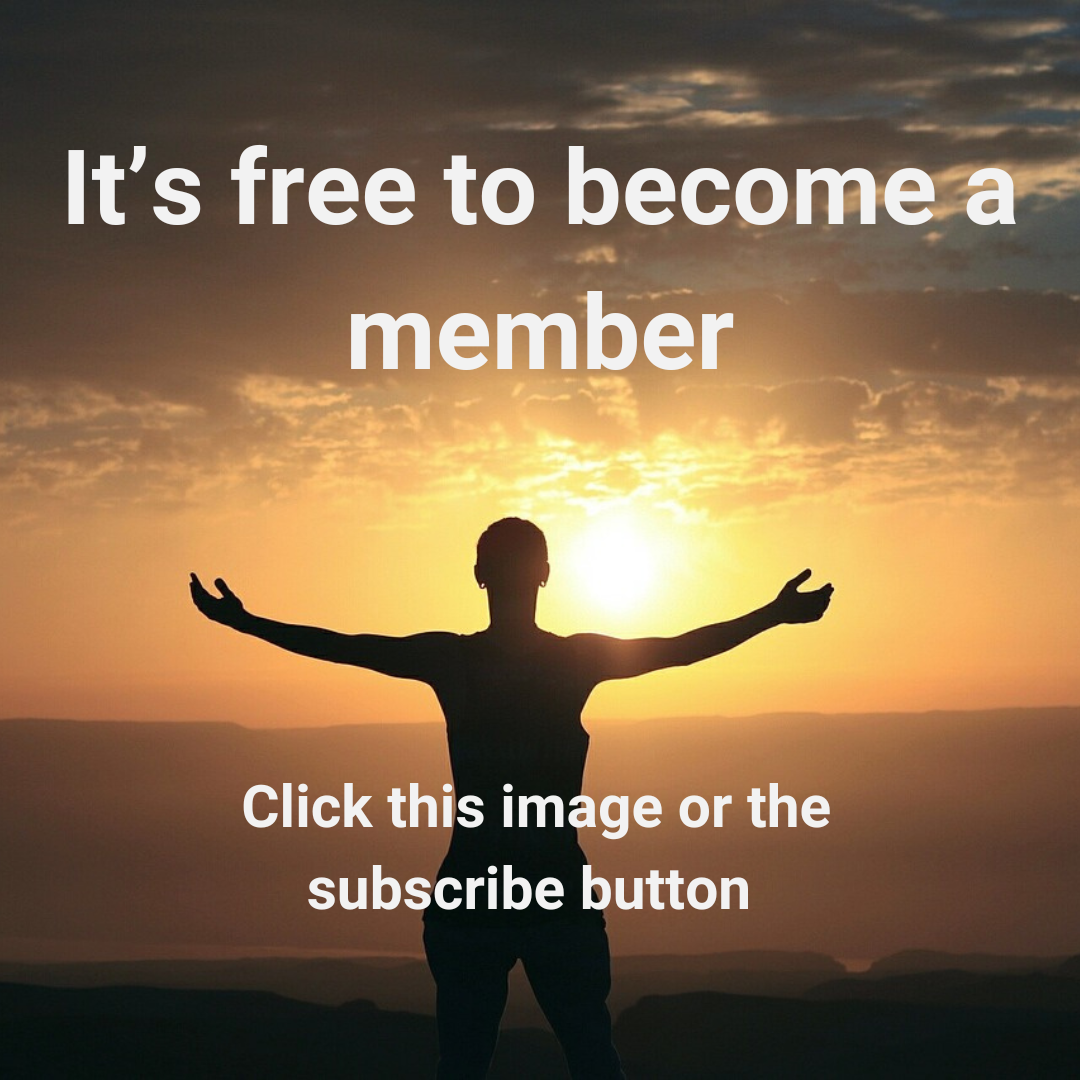
The details
With 75% of Finland covered by forests, wood is a readily available material for construction. Finland is aiming to reach carbon neutrality by 2035 and given that wood has 20% to 30% lower greenhouse gas (GHG) emissions than concrete/steel/brick buildings, its usage will likely grow.
Developers in Finland are increasingly swapping concrete and steel for wood. The Federation of Finnish Working Industries’ data suggests wood is a key material in 4% of apartments and 16% of commercial buildings. Wood City in the city centre of Helsinki comprises hundreds of wooden apartments, the wood lined headquarters of gaming company Supercell, as well as a number of buildings under construction including the new offices of WithSecure which will be constructed of engineered wood.
Why this is important
One part of the solution to some of our hard to decarbonise sectors, so cement and steel, could be to use different materials in construction. Timber is a material we have used for thousands of years, and technological improvements, such as glulam (glued and laminated) beams, mean that it can be used as a structural element, allowing the construction of taller timber commercial and office buildings. So, what are the opportunities and the barriers to a wider adoption?
First, opportunity. The built environment is an important area of focus for sustainability investing. It represents over one third of global final energy use, generates nearly 40% of energy-related GHG emissions (which in themselves are 75.6% of total GHG emissions) and consumes 40% of global raw materials. It is now estimated that over 56% of the world’s population lives in cities and that by 2050 more than two-thirds of the world population will live in urban areas putting upward pressure on the contribution of the built environment to resource consumption, GHG emissions and ultimately anthropogenic global warming.
A 2019 study published in the Journal of Building Engineering found that replacing concrete and steel with a hybrid cross-laminated timber (CLT) in the building structure presents significant environmental benefits including “an average of 26.5% reduction in global warming potential.” Other countries in addition to Finland are pushing ahead. For instance, France requires new publicly funded buildings to comprise 50% timber or natural materials by 2022.
Finland’s Climate Change Act which was approved earlier this year has them aiming to be carbon negative by 2040, joining Bhutan, Suriname and Panama that have already been declared carbon negative. Finland’s forests will be an important part of their toolkit as will reducing emissions from agriculture, transport, building and waste industries, and changing their power generation mix. However, as more trees are removed for building, as well as for other purposes such as paper, then replanting logged areas needs to be carefully managed. In 2021, the land use sector was for the first time a net source of emissions at 2.1 million tonnes of CO2 equivalent, which Statistics Finland believe was due to “... fellings implemented at a high level and the falling trend of annual increment of growing stock.”
There are a number of other natural resources that could be used in place of wood including hemp, cork (ok so that is from a tree but the bark rather than the core), kokoboard (made from otherwise discarded peanut shells, rice straw, husk and coconut dust) and bamboo. As a building material, bamboo is an interesting one, although not without its own controversies. On the plus side it shows comparable strength by comparison to engineered wood products and it grows much faster than wood (one millimetre every ninety seconds). It also has good thermal performance owing to its naturally cross-laminated fibre structure.
What other issues does this raise?
We tend to think of timber as mainly being used in residential buildings, but it’s also used in commercial premises. 80 M Street SE in Washington DC was opened in September comprising three floors and 108,000 sq ft of commercial office space - built using over 1,300 tons of mass timber. The Ascent MKE in Milwaukee, Wisconsin is 87 metres high, pipping Norway’s Mjosa Tower to be the tallest timber building. So, it’s not just a material we can use to build our homes.
Timber use in low rise residential buildings is already increasing. Here it’s relatively uncontroversial (we will talk about sustainable sourcing in another blog) and its advantages are largely about speed of construction and hence cost. It has been estimated that using this approach can take 10 weeks off the normal 26 week build time. Being able to assemble the timber components in a controlled factory environment and then truck them to site for quick erection is a major advantage.
Where the use of timber becomes more problematic is in multi-story structures, where it needs to retain higher levels of structural strength. Here the main concern is safety, particularly as it relates to fire. The aftermath of the Grenfell disaster saw the UK government impose limits on the use of combustible materials in residential buildings higher than 18m, which was subsequently extended to 11m high buildings in June of this year.
Let’s start with the challenges to an increased use of timber in tall buildings. The main ones are out of date building standards to allow for charring in fires (timber members are designed such that the undamaged timber remaining beneath the char layer is able to support the required loads), the possible delamination of engineered timber in serious fires (destroying structural strength), and the risk of external fires spreading faster (fires in buildings with large amounts of exposed timber surfaces lead to larger and more extensive external flames projecting from window openings etc).
All of these challenges are technically solvable. There is a major international effort underway to develop a state-of-the-art guide for the fire design of tall timber buildings. This is due to report back this year, and it will enable global best practice to be included in national building codes and standards.
But this only gets us part of the way there. The real problem, as exposed by the UK Grenfell disaster and others, is the gap between standards and what actually gets built. Put simply, engineers and architects cannot control the detail of construction quality (we argue they should, but that is another debate). To illustrate the harm that poor build quality on site and compliance with codes can cause, let’s use a real example.
Timber frame buildings are supposed to contain cavity barriers – typically small rolls of mineral wool insulation which prevent hot gases from a fire entering a cavity and limit it from spreading if it does. For these to work, they must be fitted correctly on site. Following concerns about quality, one of the UK’s largest house builders, Persimmon, commissioned Stephanie Barwise QC to carry out a review of its operations. She concluded the builder had “a nationwide problem of missing and/or incorrectly installed cavity barriers in its timber-frame properties”. This was said to be “a manifestation of a lack of supervision and inspection of the way in which building work is carried out”. If this is not done properly, all of the work done on building standards and codes is wasted. And timber framing will not deliver the benefits, both in terms of building cost and environmental impact, that it can.
What is the solution?
It’s complicated but at the same time simple. We need to spend more on skilled and trained builders and inspectors. and we need to ensure standards are being followed. What can we do as investors - demand action from the management teams and boards of the companies we are, or want to be, invested in. This is potentially a real engagement win, get involved in understanding the problem and then push to make the solutions happen. And keep monitoring.
Something a little more bespoke?
Get in touch if there is a particular topic you would like us to write on. Just for you.
Contact us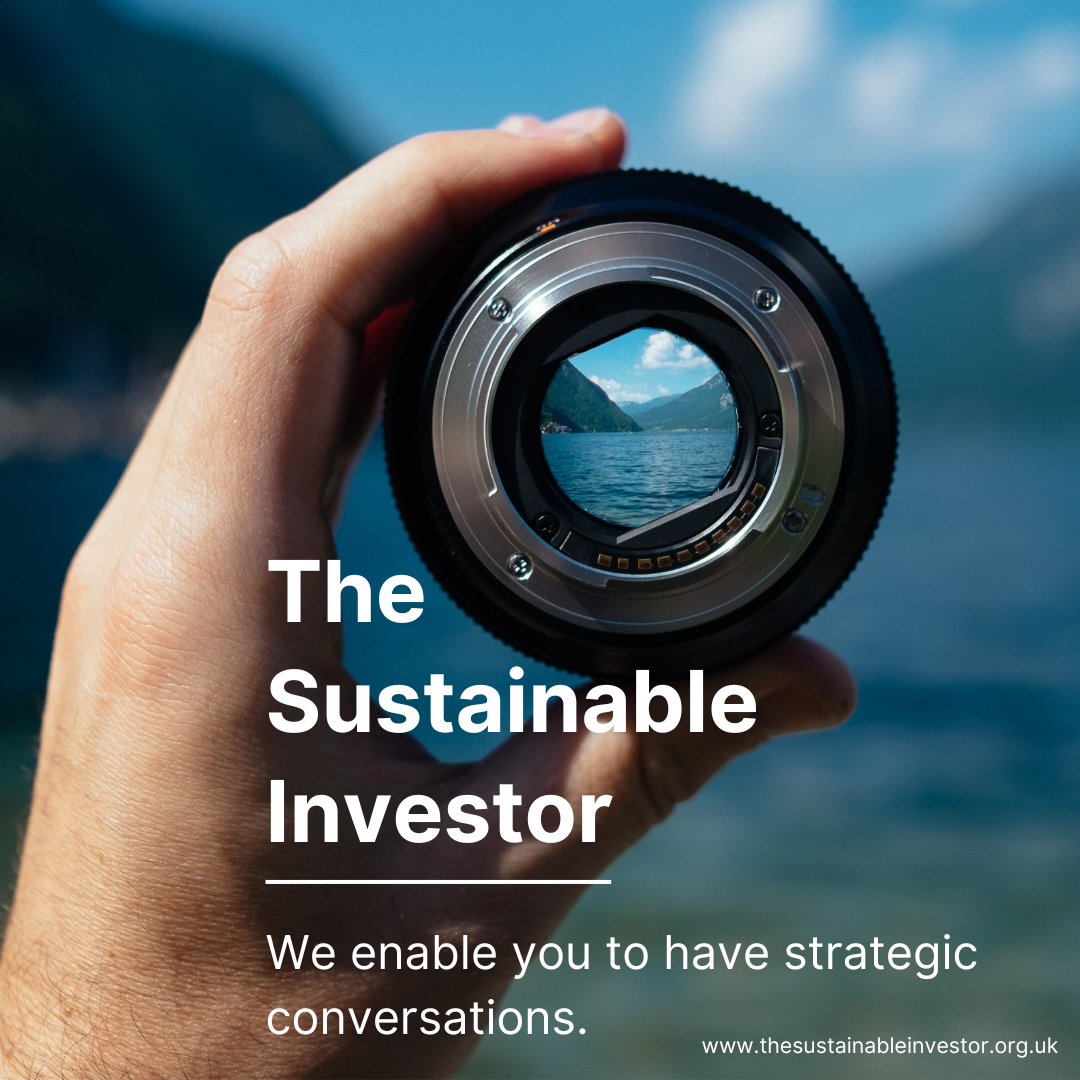
Please read: important legal stuff.