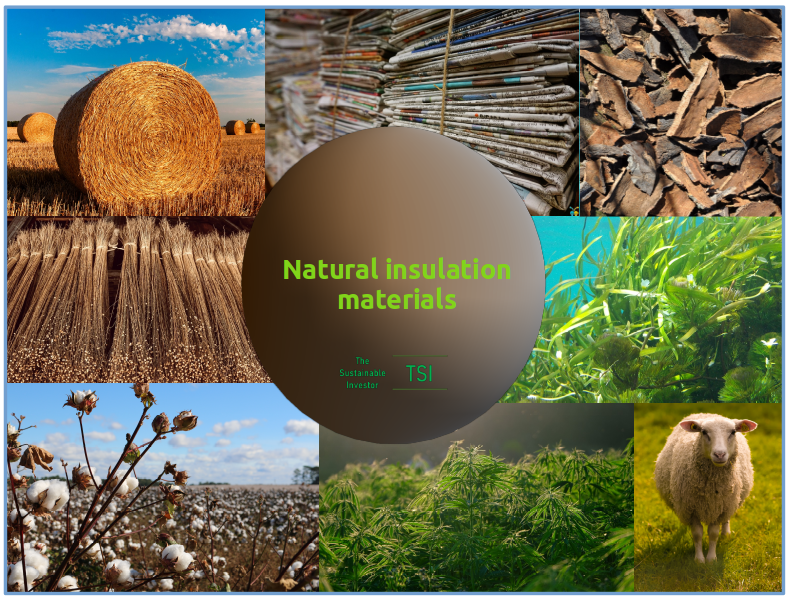
How do nature's insulation materials compare?
Nature has provided insulating materials in the past, but modern technology could mean a return to the mainstream for a more sustainable option.
Summary: A number of natural options exist for insulating our homes that can be more sustainable and potentially as cost effective as some commonly used synthetic materials. We look at a selection of them and examples of where they are used in practice, including straw bales, cellulose, cork, wood fibre, cultivated plant fibres such as flax and hemp, recycled cotton, sheep's wool and even seaweed.
Why this is important: Conventional synthetic insulation materials are often derived from petrochemicals and thus have high embodied carbon as well as end-of-life disposal issues.
The big theme: The built environment, encompassing residential and commercial buildings, communal areas such as parks, and supporting infrastructure such as energy networks, mobility, and water supply, is an important sustainability theme. It is an integral part of societal existence and a major resource consumption problem (40% of global raw materials) and decarbonisation problem (40% of energy-related GHG emissions) that needs investor, government, business and consumer attention.
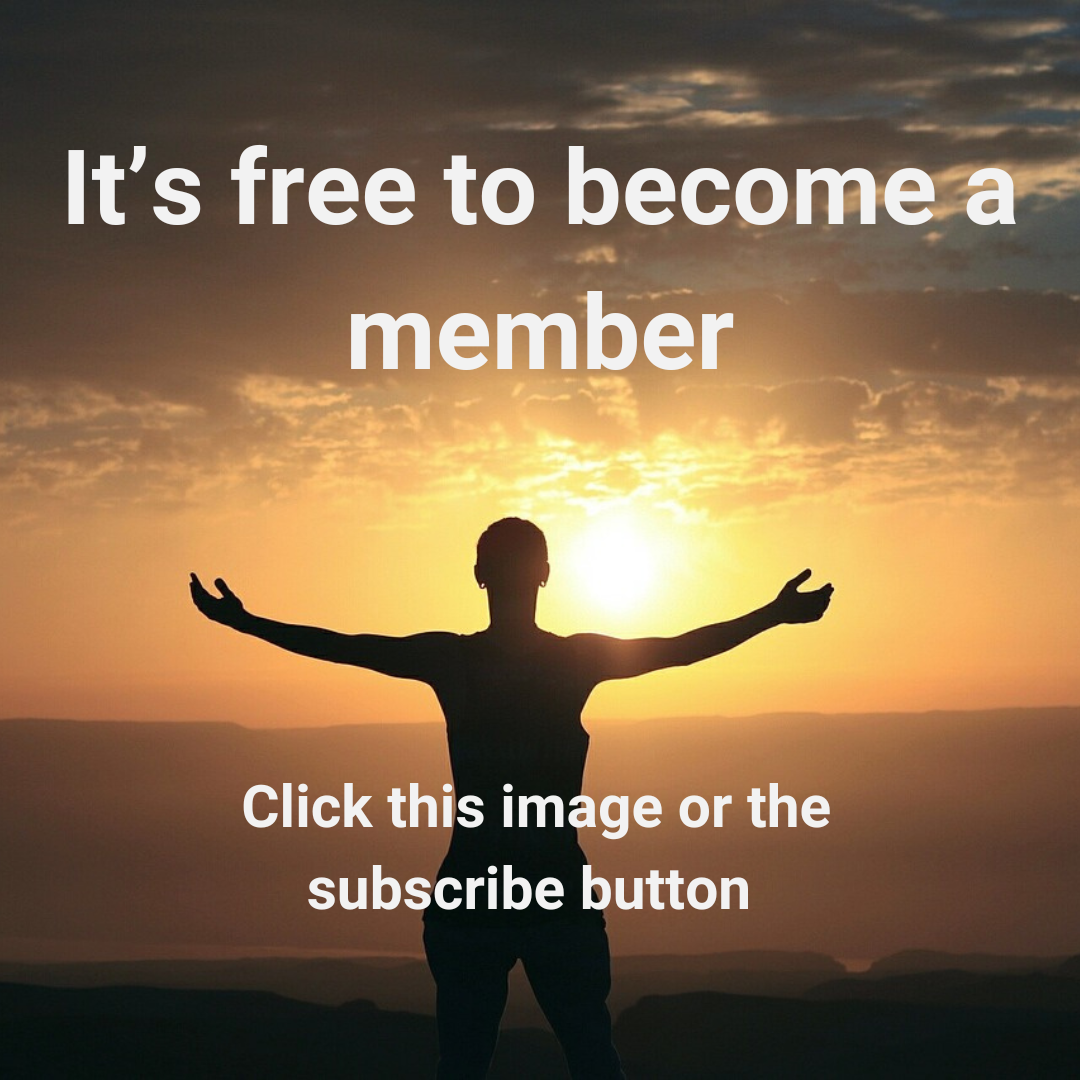
The details
Back to the future for insulation?
Currently the vast majority of insulation is made from petrochemicals. Insulation has been used for centuries to slow down the movement of heat in and out of buildings. Nature provided solutions back then and can do so now with more sustainable options. One or a combination of several materials can be used as insulation. Examples include straw bales, cellulose, cork, wood fibre, cultivated plant fibres such as flax and hemp, recycled cotton, sheep's wool and even seaweed. We introduced the topic in another blog 👇🏾
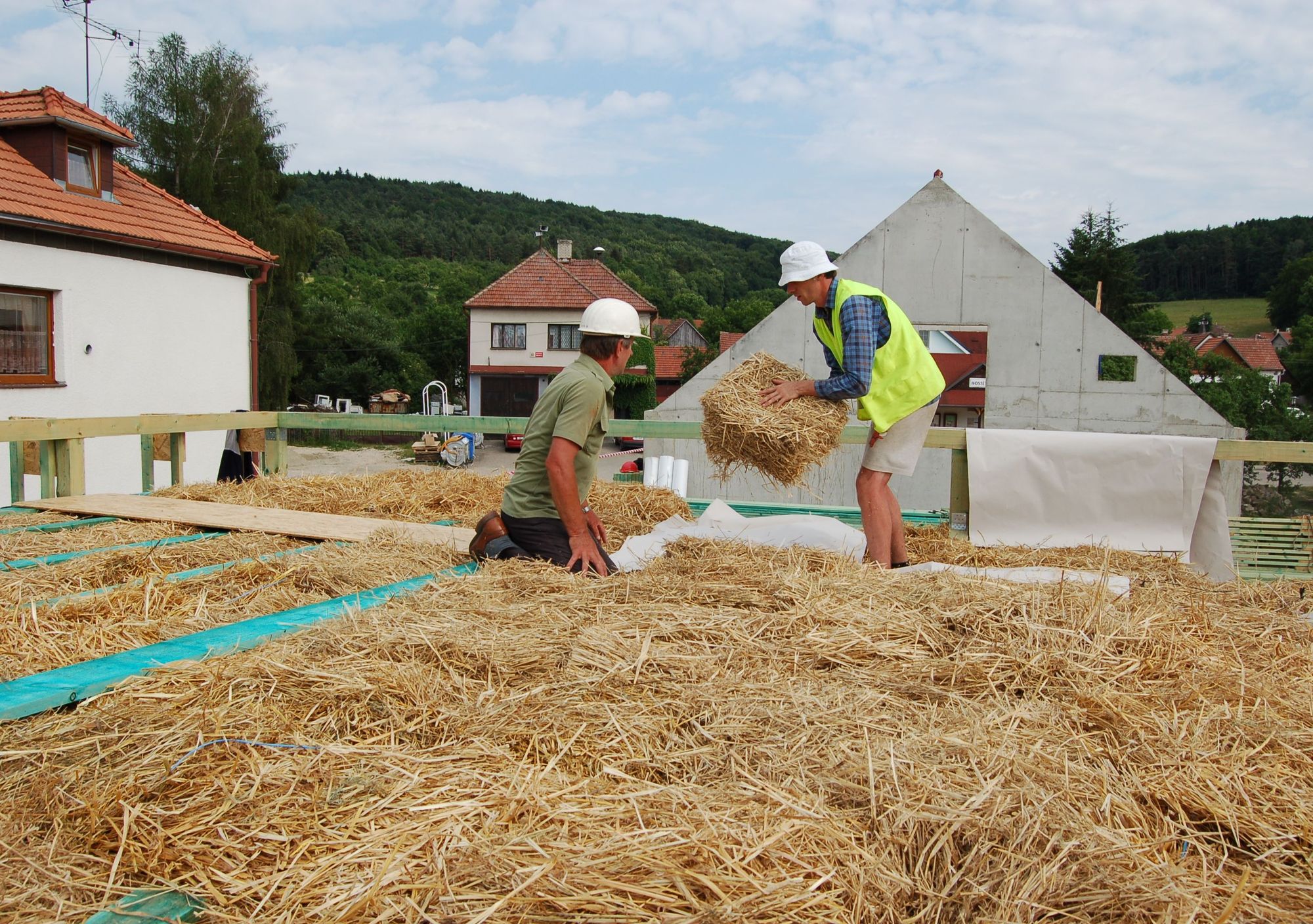
Natural materials could offer sustainable alternatives in selected cases although it is a trade-off between cost, effectiveness and aesthetics.
Let's take a closer look ...
How do different natural insulation materials compare?
As a reminder, insulating materials are rated with an R-Value which lets us know how effective they are at insulating - the higher the R-Value, the more effective the insulation. Insulation systems that combine a number of materials, typically structured together as panels that can then be fixed to walls or in roofs, can have an overall R-Value calculated. This allows architects and designers to work out the best combination for the environment in which the building is sited. Strictly speaking the 'R-Value' is an imperial system unit of measurement; the metric version is often referred to as RSI-Value.
You can find out more about R-values and other relevant variables including thermal conductivity and U-value here.
The choice of appropriate insulating material will be based on a number of factors. In addition, how that insulating material is installed is important. Air leakage, which can be a function of how tightly the material is packed, can impact overall performance as can whether ceiling joists are completely covered as heat can transfer through steel, for example.
The chart below gives a starting point for comparing cost and R-Value for consistent values.
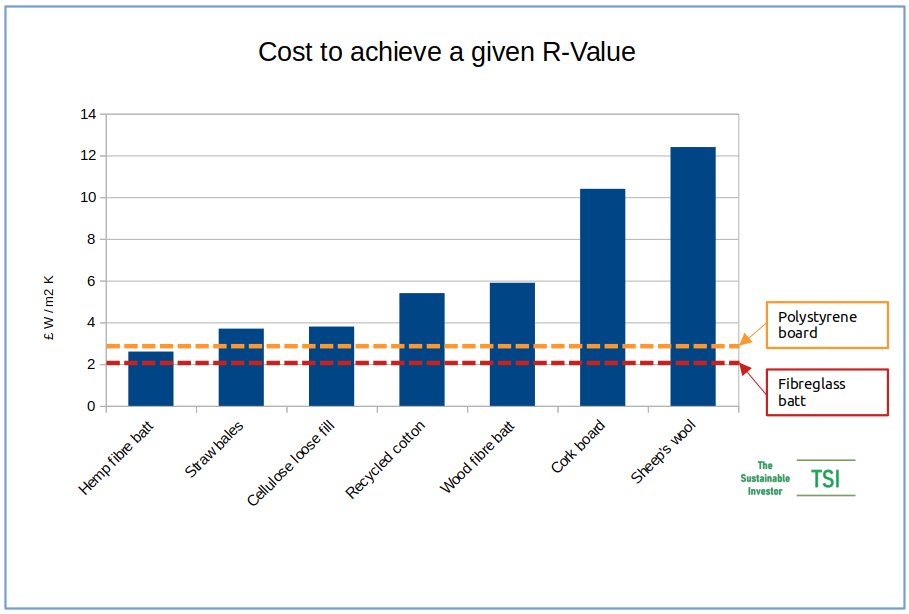
Let's look at some more characteristics of a selection of natural insulating materials including some examples of their use. There are others, including lab grown materials such as those based on mycelium (fungus) and algae, but we shall be covering those in future blogs. The materials can be 'blown in' to cavities as granulated material, as felted material called batts, or as compressed boards.
Natural materials examples
Straw Bales:
Straw bales can and have been used as a form of insulation in walls. They are readily available from agricultural waste and can be constructed into insulation systems. You can see from the chart that they are reasonably cost effective for their R-value however, often straw bales are quite thick (0.4 metres) and so not suitable for all construction. They are completely biodegradeable, but can last over 100 years once installed. Moisture can be problematic bringing with it the risk of mould and so areas of extreme humidity and rain may not be appropriate. Whilst there is a risk of fire, because straw bales are quite densely packed, fire tends to smoulder and so they can offer better fire resistance that a timber frame construction.
Wood Fibre:
Wood fibre insulation is made from recycled wood waste and can be used as rigid panels or as a loose-fill into cavities. The trees used to produce it absorb CO2 while growing and so are net carbon stores once installed. It has good acoustic and thermal insulation properties but costs quite a bit more for a given R-Value.
In Tilburg in Netherlands, The De Roomley Sports Hall was in need of maintenance and to improve its operational efficiency. As part of the move to meet the area's net-zero performance goals and sustainable construction criteria, a key upgrade was to the insulation of the building. They used prefabricated panels filled with densely-packed straw enclosed by wood fibreboard insulation. The panels were sized to fit behind the existing brick facade. The total R-Value of the 15 in / 38 cm thick panels was 46 (just over 3 per inch of thickness). The retrofit was a beneficiary of the European Regional Development Fund UP STRAW project.
Cork:
Cork insulation is made from the bark of cork oak trees and importantly you don't need to actually fell the tree to remove the bark. It is therefore very renewable. It is breathable and so will trap heat without trapping moisture which also gives it some resistance to pests. As with the straw bales it burns very slowly with no flame so has some natural resistance to fire. Cork board is relatively expensive for the insulation it provides.
'The Float' in Leiden, Netherlands is completely cladded in cork. The architects, Studio RAP chose cork as it is a "great material to manufacture digitally" and they were able to use CNC machines (Computer Numerical Control) to cut the various cork modules so that they fit seamlessly.
Cellulose:
Cellulose is the main constituent of plant cell walls and vegetable fibres. Cellulose insulation is made from recycled paper which is then treated with fire retardants. It can be blown into wall cavities or installed as batts. Cellulose has good thermal performance with high R-values and importantly cellulose is a very good air-blocker. Air leakage through cracks and gaps is thought to be responsible for one-third of an average home's heat loss. It is also a reasonably good soundproofing material.
In 2018, the Sundance Housing Co-operative based in Edmonton, Canada elected to undergo a deep retrofit of a number of its properties. One such property was a duplex home built in the 1970s. They used prefabricated wood-framed sections with an outer air barrier membrane and then filled with dense-packed cellulose insulation. For the walls, the eight inches provided an R-value of 26 and for the cellulose insulation in the roof trusses an R-Value of 50.
Cultivated plant fibres:
A number of cultivated plants can be used to make insulation. We are going to touch on two of those. Flax (or Linseed) fibres and hemp fibres are both resistant to mould and pests and have good thermal insulation properties. Flax used in insulation is derived from the stalk of the linseed plant which has low economic value. Hemp grows very fast, consumes very little water and sequesters more carbon than it consumes during its construction as an insulation material. Both materials can see their insulating properties compromised by moisture and are flammable if untreated.
Interesting to note that in terms of cost effectiveness, hemp fibre compares favourably with commonly used synthetic materials such as fibreglass but the scale is not there yet.
Hemp has also been used as a mixture with hydrated lime (from limestone) and water to make 'hempcrete'. It has an R-Value per 100mm of thickness of around 2 which is a little lower than hemp fibre batt but it is more versatile.
A good example of a sustainable development is the use of hemp in the buildings at a hemp farm - Flat House at Margent Farm
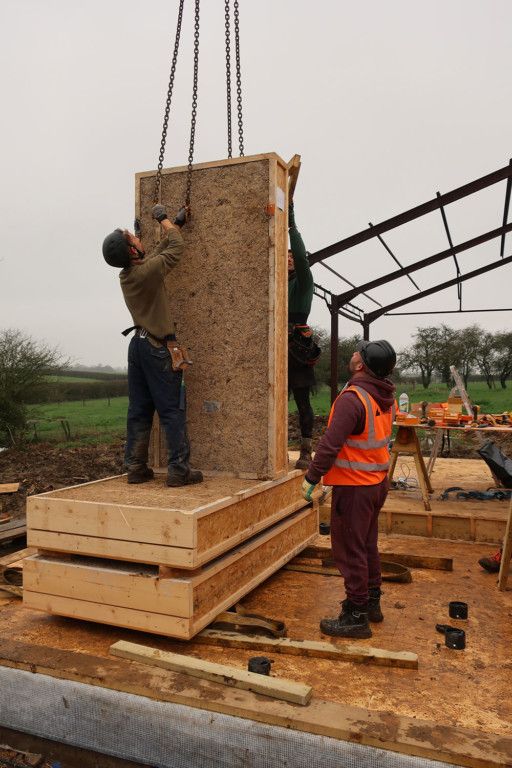
Cotton:
Recycled cotton fibres, such as denim, can be used as insulation. They are treated with borates to make them fire-resistant and fungi/bacteria-resistant. Cotton insulation has good acoustic and thermal insulation properties. It is easier to handle than fibreglass insulation as it doesn't release irritant fibres in the air. It is not as cost effective as the more commonly used synthetics. However, cotton insulation can be prone to water damage which ultimately reduces its insulating properties.
It can also reduce the amount of cotton textile going to landfill as part of the 'reuse' economy. It is also not available at scale yet.
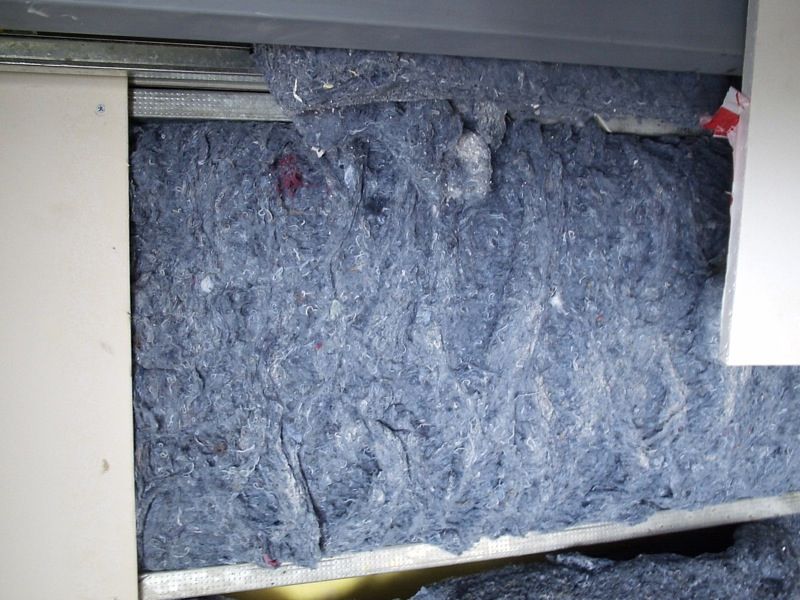
Sheep's Wool:
Wool fibres form millions of very small air pockets that trap air and slow down the transfer of heat. It is what allows sheep to live in sometimes inhospitable environments. It is a very sustainable choice as it is abundant, continuously renewable, lasts for decades on site and can simply be composted at the end of its life. Sheep's wool uses a fraction of the energy to produce compared with synthetics like polyurethane foam - less than six percent. It is breathable and absorbs moisture, able to release it back into the air as heat. In this way it can regulate temperature well. However, it is expensive comparatively and so is best used close to sheep mills.
Cultybraggan Camp is a former World War II prisoner of war camp in Perthshire, Scotland. Its individual 'Nissen huts' are now available to rent as holiday homes. In 2014 Hut One was refurbished using a number of different insulation systems including sheep's wool.

Seagrass and seaweed
Like hemp and bamboo, seaweed and seagrass are also very fast growing. They are renewable, biodegradeable and have the potential to sequester carbon during their growth. Seaweed-based insulation typically involves processing seaweed into a fibrous form and combining it with other natural fibres or binders to create insulation panels or mats. It is not widely used at the moment, but there are some interesting examples, including the 'seaweed houses' on the Danish island of Laeso. Eel grass is technically not a seaweed (it is a seagrass which is vascular plant rather than an algae).
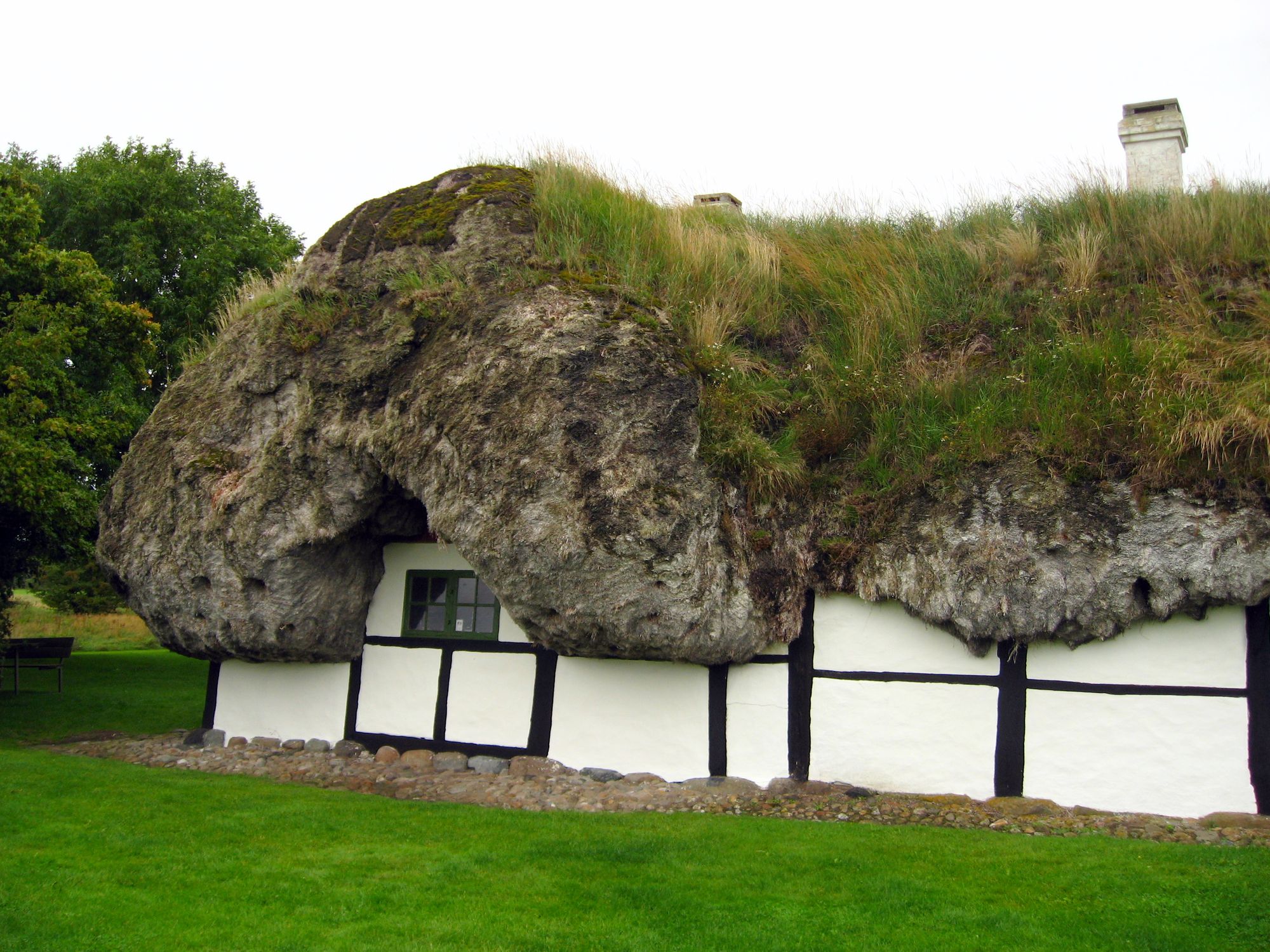
Global warming potential
An important consideration in the choice of insulation is not just what it does for the building during operation but also the impact it can have on embodied carbon (~11% of energy-related GHG emissions) both at the initial construction phase and also in retrofitting or repurposing existing buildings.
A research piece from RMI looked at the performance of a number of different insulation systems in this regard. You can see from the table below that cork board, wood fibre board, cellulose and hemp fibre (both in hempcrete and batt) actually store carbon in situ - effectively turning a building from a carbon liability to an asset!
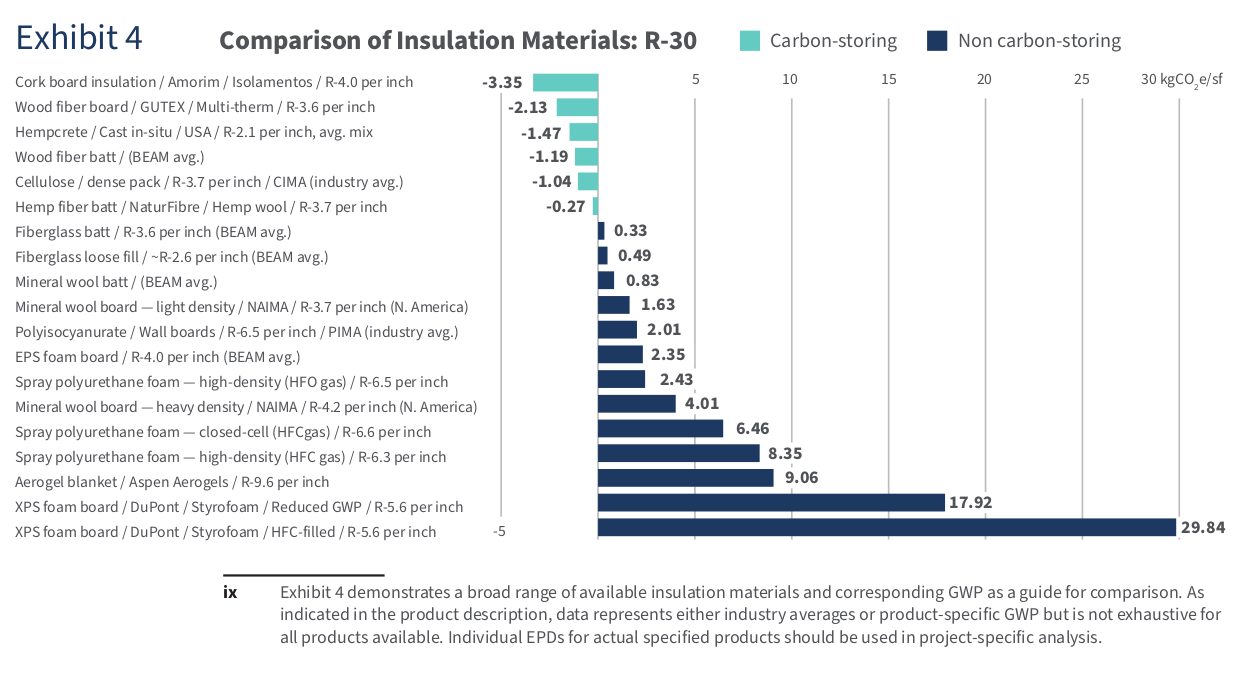
We discussed RMI's work further in this blog 👇🏾
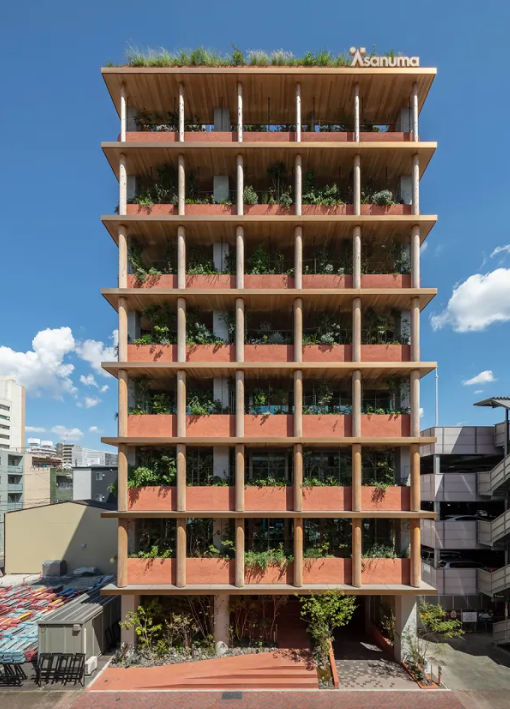
Conclusion
Currently the vast majority of insulation is made from petrochemicals. Insulation has been used for centuries to slow down the movement of heat in and out of buildings. Nature provided solutions back then and can do so now with more sustainable options. As well as regulating temperature and reducing our need for energy hungry heating and cooling systems, they can also be a lower embodied carbon option - even continuing to act as carbon stores. Building codes and education need to catch up too so that a greater choice of materials are available for builders and these insulation systems can be installed in appropriate settings.
Something a little more bespoke?
Get in touch if there is a particular topic you would like us to write on. Just for you.
Contact us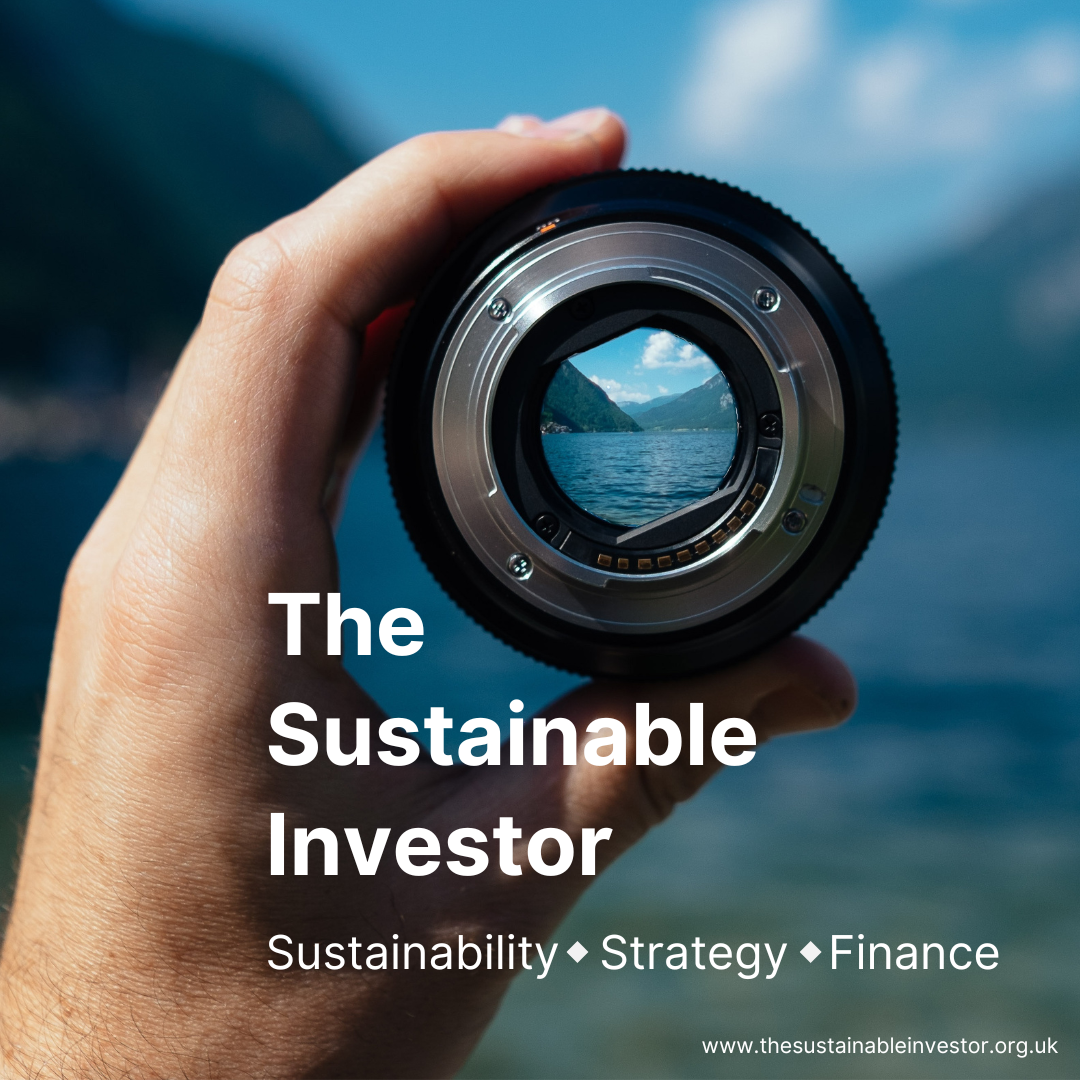
Please read: important legal stuff.