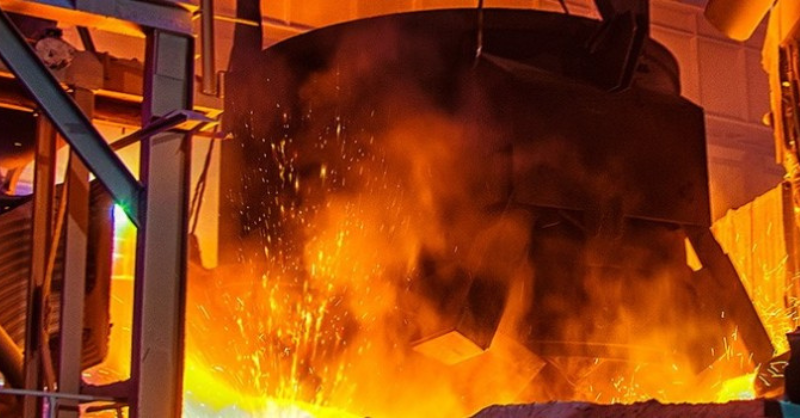
Have we finally found a zero carbon cement solution?
What if we could take demolition concrete and turn it back into new cement. And do it piggy backing off the process for making greener steel - the Electric Arc Furnace. Wouldn't that be good news.
Concrete is an essential element in our modern society, but it's production (specifically the cement we use to make it) is a high emitter of Green House Gases (GHG's). The challenge is in the clinker, the essential ingredient in cement. We can reduce the amount of clinker we use, but it's currently almost impossible to replace it. But a team led by the University of Cambridge might just have the solution.
Now the big challenge is to scale it up, to take it from a pilot to commercial production. But it could potentially contribute up to one third of UK cement demand, and be scalable worldwide.
You might be wondering why a cement story has an image of an Electric Arc Furnace and not the traditional rotary kiln? Because that's where the chemical magic happens. The solution is both simple and complex .....
This is a What Caught Our Eye story - highlighting reports, research and commentary at the interface of finance and sustainability. Things we think you should be reading, and pointing out the less obvious implications. All from a finance perspective.
It's free to become a member ... just click on the link at the bottom of this blog or the subscribe button. Members get a summary of our weekly posts, including What Caught Our Eye and Sunday Brunch, delivered straight to your inbox. Never miss another blog post !
Recycling old concrete to produce new cement
We would struggle to run our economy without cement. It's what we use (by adding sand, aggregate and water) to make concrete - for our buildings, for foundations for things like wind turbines, and for hydro dams. I worked as an engineer for many years before moving into finance, and reinforced concrete is an amazing material. But, the production of cement is also a massive generator of GHG's.
The production of cement, accounts for between 5-8% of global GHG emissions. This is a similar scale to the GHG emissions of passenger cars. And so it's a challenge worth solving.
The big contributor to cement's GHG emissions is the making of clinker, the critical raw material. And while we currently have ways of reducing the amount of clinker we use to make cement, we cannot eliminate it. So we can make lower carbon cement but not zero carbon.
So the solution to making zero carbon cement is in the clinker.
If you want to understand better how we make cement, this blog that we wrote back in May 2023 is worth a read.
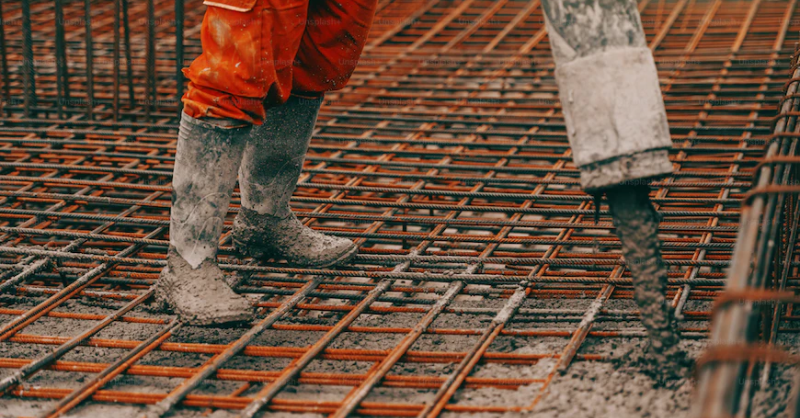
What has changed since we wrote this blog last year? It turns out a lot has changed.
Researchers at the University of Cambridge identified that clinker had similar chemical characteristics to steel slag. When we make steel, we use what is called a flux to purify the molten metal. This slag removes the impurities and when it hardens we get slag.
If you want to better understand the steel making process, and the essential difference between making steel with a blast furnace vs what is called an Electric Arc Furnace, this blog we wrote in Jan 2023 is also worth a read.
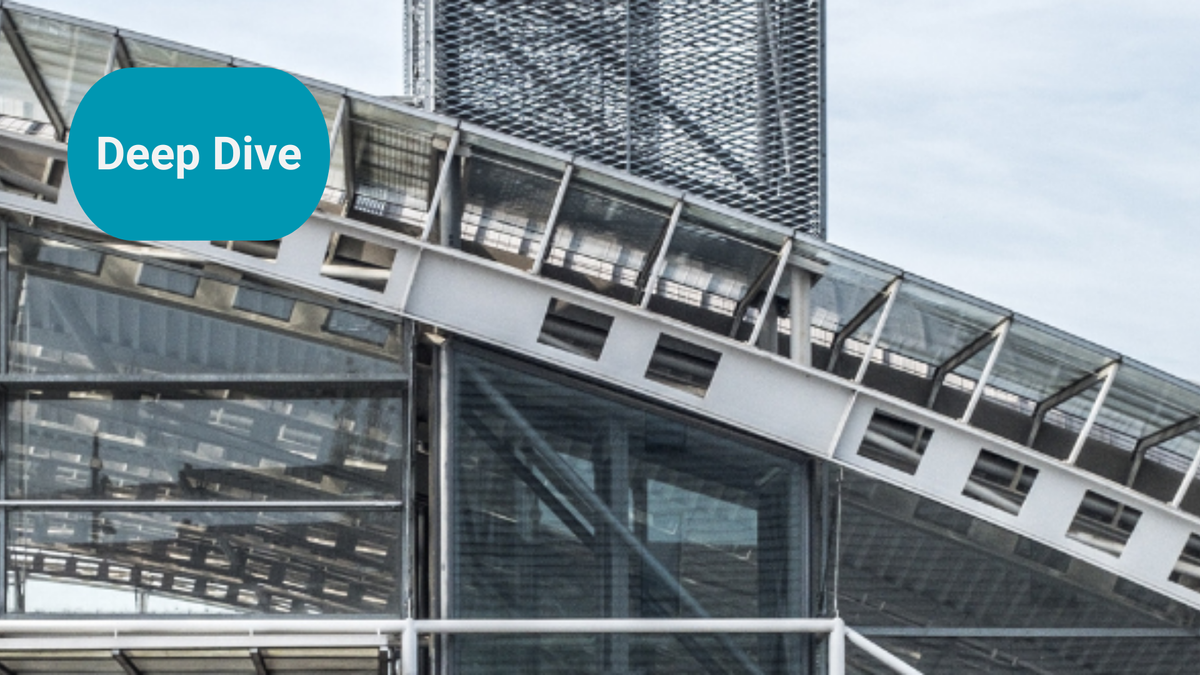
So, cement clinker is similar to steel slag. This is then where the really clever bit came in.
The team identified that if you took old concrete (from demolished buildings etc) and crushed it very finely, you could separate out the cement dust. And that if you then put that in an Electric Arc Furnace along with scrap steel, at the end you get steel plus a slag that can be used to make new cement.

So we go from demolition concrete to new cement. And all piggy backing off the production of steel. So no extra energy requirement.
It's worth repeating, we take the normal process for making steel in an Electric Arc Furnace, but instead of the traditional flux, we use our ground up old cement dust. And that produces steel and cement.
And if we use green electricity to power the Electric Arc Furnace (and the crushing process), we can make (almost) zero carbon cement. And it recycles demolition concrete as well.
Does it work - yes. Industrial scale trials started in May at a 150t furnace owned by Celsa UK, following the successful completion of pilot trials using CEC’s method at a 7t electric arc furnace owned by the Materials Processing Institute.
Is this a total solution. No. It only works in an Electric Arc Furnace, which uses scrap steel as it's raw material. This is a constraint. But even with this the researchers estimate the process could produce c. 1/3 of the UK's cement requirements.
How long will this take to scale up - maybe as long as a decade. It may turn out to be harder to scale up, but it's a really encouraging start.
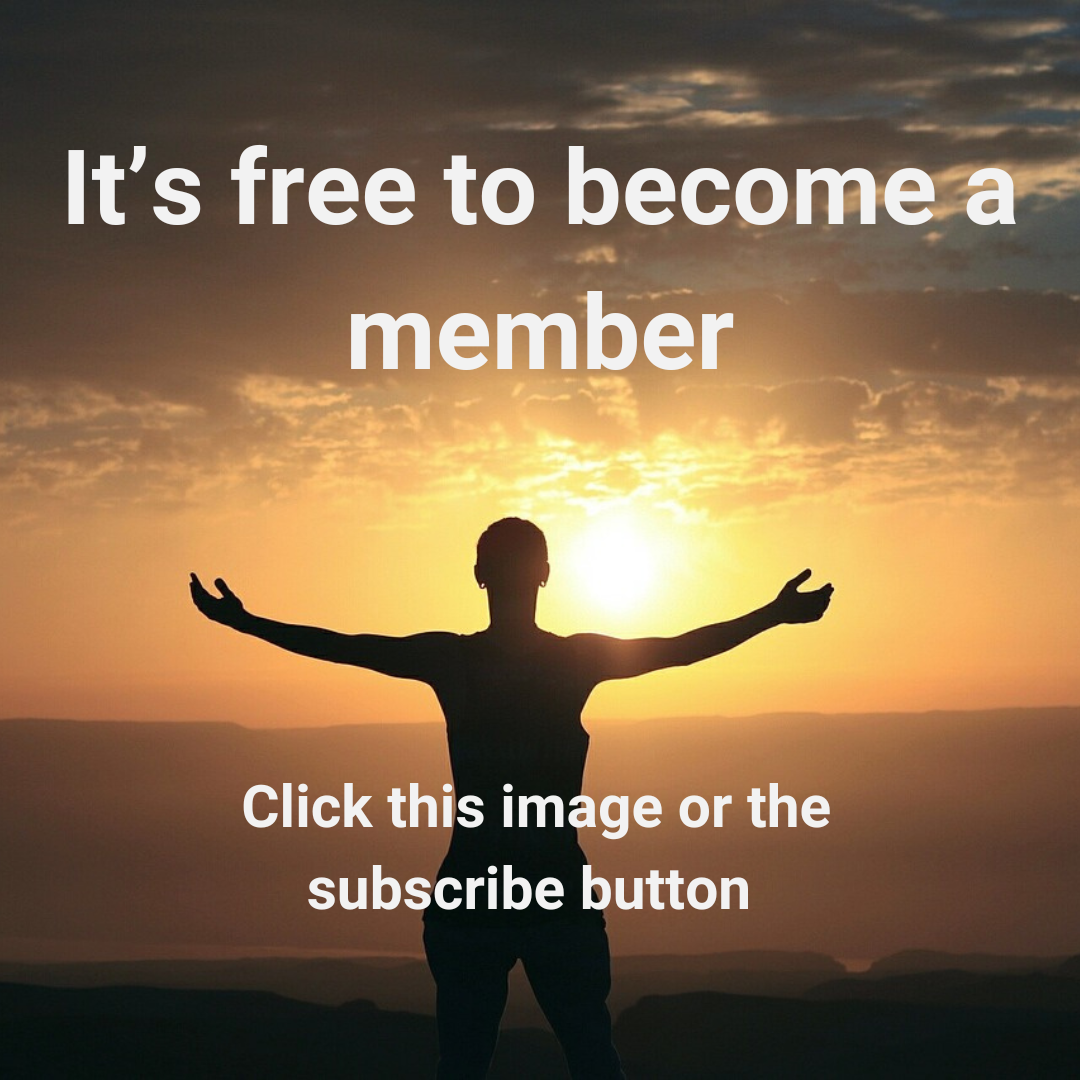
Please read: important legal stuff.